What innovations are driving the future of gearbox designs?
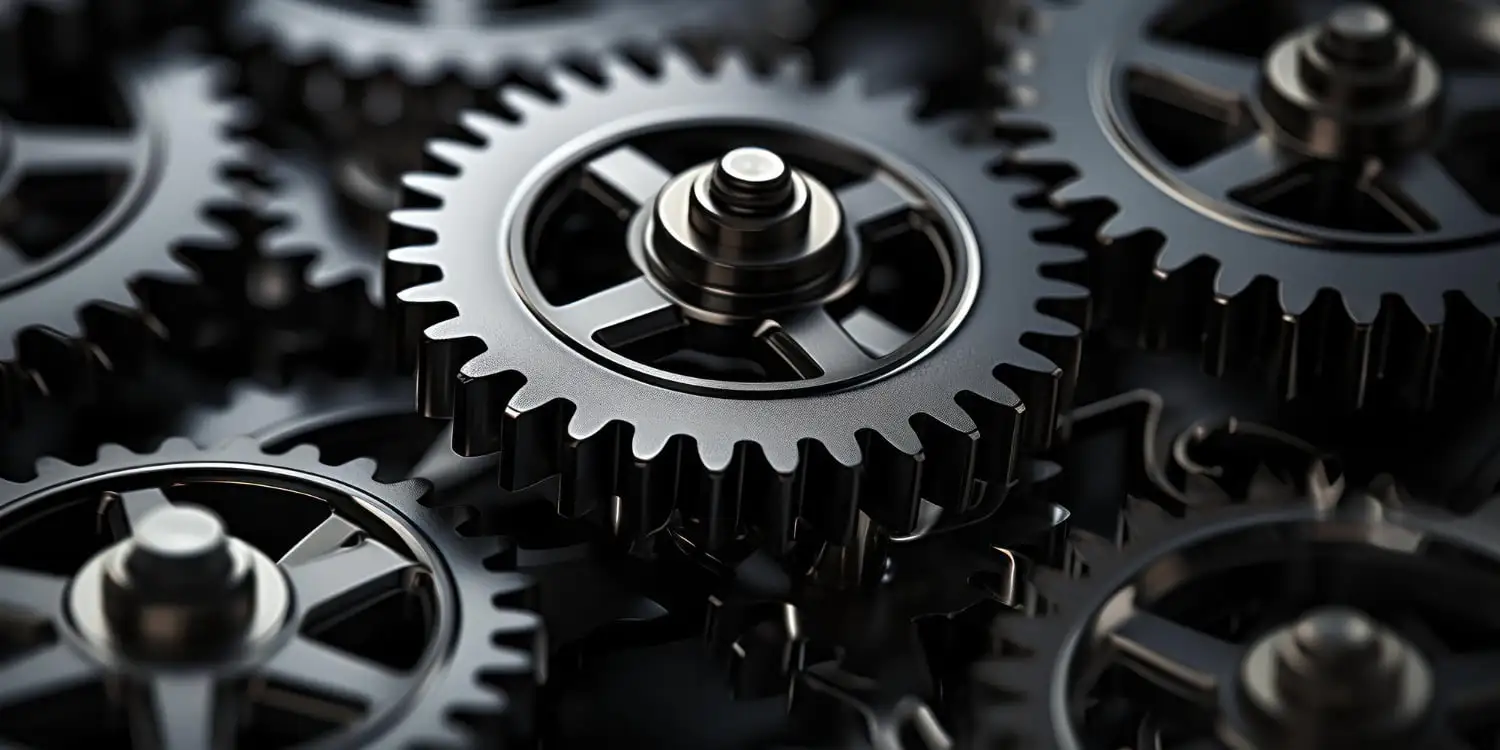
The world of mechanical engineering is constantly evolving, and one area seeing remarkable change is gearbox design. Gearboxes are critical components in a wide range of industries, from automotive to industrial machinery. As technology advances, so too do the innovations that shape the future of gearbox design. A reputable gearbox manufacturing company is at the forefront of these advancements, ensuring that their products provide more efficiency, durability, and precision in their operation. This article takes a closer look at the cutting-edge innovations that are driving the future of gearboxes.
The Evolution of Gearbox Technology
Gearboxes have been around for centuries, but their designs have become more sophisticated over time. Initially, gear systems were simple, but with the advent of new technologies, manufacturers began pushing the boundaries of what gearboxes could do. Today, engineers focus on enhancing performance, reducing noise, and increasing efficiency while ensuring that gearboxes are smaller and more lightweight.
3D Printing and Gearbox Prototyping
One of the most significant innovations in gearbox design is the use of 3D printing. This technology allows engineers to prototype new gearbox designs quickly and cost-effectively. Instead of spending weeks or months building prototypes using traditional methods, 3D printing enables manufacturers to test and refine designs in a fraction of the time. By using 3D-printed parts, engineers can create complex geometries that were previously impossible or too expensive to manufacture.
Lightweight Materials for Enhanced Efficiency
Another key development in gearbox technology is the use of lightweight materials. Traditional gearboxes were often made from heavy metals, which limited their efficiency and performance. Today, engineers are turning to materials like carbon fiber, titanium, and advanced polymers to create lighter, stronger, and more durable gearboxes. These materials not only reduce the weight of the gearbox but also improve fuel efficiency in applications like automotive and aerospace.
Digital Twin Technology
Digital twin technology is an exciting innovation that is revolutionizing gearbox design and maintenance. A digital twin is a virtual replica of a physical asset, like a gearbox, that can be monitored and analyzed in real time. By collecting data from sensors embedded in the gearbox, engineers can create a digital representation of its performance and behavior. This data allows for predictive maintenance, which helps identify potential issues before they lead to failure. Digital twins also enable engineers to simulate different conditions and stress test gearbox designs, leading to more efficient and reliable products.
Artificial Intelligence and Machine Learning
Artificial intelligence (AI) and machine learning (ML) are having a significant impact on gearbox design. These technologies enable systems to analyze vast amounts of data and identify patterns that humans may not notice. In gearbox design, AI and ML can help optimize gear ratios, predict wear and tear, and enhance the overall performance of the system. These technologies also assist in automating the design process, reducing human error, and speeding up the time it takes to develop new gearbox models.
Variable Gear Ratios
Variable gear ratios are an innovation that has gained popularity in recent years, especially in the automotive industry. Traditional gearboxes rely on a fixed gear ratio, which means the gears only operate at certain speeds. Variable gear ratios, on the other hand, can change dynamically to adapt to different driving conditions. This allows for smoother acceleration, better fuel efficiency, and improved performance. Gearboxes with variable gear ratios are becoming more common in electric vehicles (EVs) and hybrid cars, where efficiency and power output are key considerations.
Electromechanical Systems
Electromechanical systems are transforming the way gearboxes function. These systems use electric motors in combination with traditional mechanical gears to create more precise and efficient gear shifts. In applications like robotics and automation, electromechanical gearboxes can deliver faster response times and better control. The ability to electronically control the gearbox’s movements allows for more accurate adjustments, reducing the risk of mechanical failure and improving overall performance.
Smart Sensors for Real-Time Monitoring
The integration of smart sensors into gearbox designs is another key innovation. These sensors provide real-time data on temperature, pressure, vibration, and other critical factors that impact the performance of the gearbox. With this information, manufacturers can detect early signs of wear and tear, optimize operating conditions, and reduce downtime. Smart sensors also play a vital role in the development of predictive maintenance systems, where gearboxes are monitored continuously to prevent unexpected failures.
Modular Gearbox Designs
Modular gearbox designs offer greater flexibility and customization. By using interchangeable components, manufacturers can create gearboxes tailored to specific applications without having to build an entirely new system from scratch. This innovation helps reduce costs and manufacturing time while offering a higher level of customization for different industries. Modular designs are particularly useful in sectors like robotics and automation, where flexibility is crucial for adapting to changing demands.
Sustainability and Green Technology
Sustainability is becoming an increasingly important factor in gearbox design. Manufacturers are focusing on creating more energy-efficient gearboxes that contribute to reducing carbon footprints. Innovations like regenerative braking systems in electric vehicles (EVs) rely on advanced gearbox designs to convert kinetic energy into electrical energy. Additionally, designers are using eco-friendly materials and optimizing gearbox performance to minimize energy loss, contributing to the overall goal of a more sustainable future.
The Future of Gearboxes: What’s Next?
Looking forward, the future of gearbox design will likely involve further advancements in automation, smart technology, and materials science. As industries continue to push for greater efficiency, lower environmental impact, and enhanced performance, we can expect even more groundbreaking innovations in gearbox technology. The integration of renewable energy systems, automation, and even more advanced AI could further revolutionize how gearboxes are designed, manufactured, and maintained.
Conclusion
Innovations in gearbox design are paving the way for more efficient, durable, and customizable systems. From 3D printing and lightweight materials to AI and digital twins, the future of gearbox technology looks promising. As industries seek higher performance and more sustainable solutions, the next generation of gearboxes will continue to evolve and meet the challenges of the modern world. These advancements not only promise better products but also more efficient manufacturing processes, making the future of gearbox design an exciting one.