Best Practices for Digitizing Large Embroidery Designs
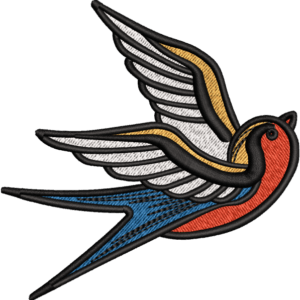
Embroidery digitizing is an intricate art that involves converting creative designs into digital formats readable by embroidery machines. When working with large designs, the process becomes even more complex. Proper techniques and strategies are essential to ensure high-quality, seamless stitching. This guide provides detailed best practices for digitizing large embroidery designs using a digitizer for embroidery software and highlights key considerations to achieve professional results.
Why Focus on Large Embroidery Designs?
Large embroidery designs are common in projects like banners, jacket backs, and home décor items. These designs require extra attention to detail because:
- They cover extensive areas, which increases the risk of distortions or thread breaks.
- Complex elements like shading and gradients demand careful planning for consistency.
- Fabric stability becomes crucial for maintaining alignment and quality.
By understanding and following the best practices, you can effectively digitize embroidery for large-scale projects while ensuring durability and precision.
Key Challenges in Digitizing Large Embroidery Designs
Before diving into the practices, it’s essential to understand the challenges:
- Fabric Shifting: Larger areas increase the chance of fabric movement during stitching.
- Thread Tension Issues: High stitch density can cause thread breaks or uneven stitches.
- Design Distortion: Improper planning can result in skewed or misaligned elements.
- Machine Limitations: Certain embroidery machines may not support very large hoops or intricate designs without splitting files.
Best Practices for Digitizing Large Embroidery Designs
1. Choose the Right Software
Selecting the right digitizer for embroidery software is the first step. Ensure the software:
- Supports large design sizes.
- Allows for splitting designs into multiple sections for machines with smaller hoops.
- Offers advanced tools like stitch simulation and density adjustment.
Some popular options include Wilcom, Hatch Embroidery, and Brother PE-Design.
2. Plan the Design Layout Strategically
When working with large designs, thoughtful planning is essential. Start by:
- Breaking the design into manageable sections or layers.
- Defining the sequence of stitching to avoid overlaps and puckering.
- Identifying areas that need underlay stitches for added stability.
Pro Tip: Divide the design logically, ensuring elements flow seamlessly when stitched.
3. Optimize Stitch Types
Choosing the appropriate stitch types can significantly impact the quality of the final output. For large designs:
- Use Fill Stitches: Ideal for large, solid areas.
- Combine Satin and Run Stitches: Use satin for borders and run stitches for fine details.
- Apply Gradient Techniques: For shading effects, adjust density gradually to create a smooth transition.
4. Manage Stitch Density
Proper stitch density ensures the design is visually appealing and structurally sound. For large embroidery designs:
- Avoid excessive density to prevent thread breaks and fabric puckering.
- Balance density settings for uniform coverage without gaps.
- Adjust density for specific fabrics to account for their stretch and thickness.
5. Use Proper Underlay Stitches
Underlay stitches act as the foundation of the design. For larger projects:
- Choose Edge Run Underlay: This provides stability for outlines and borders.
- Add Zigzag Underlay: Ideal for anchoring large areas.
- Ensure underlay stitches don’t interfere with top stitching.
6. Test on Fabric Swatches
Before stitching the final piece, test the digitized design on similar fabric. This helps:
- Identify any potential alignment or tension issues.
- Check the overall appearance and adjust elements if necessary.
- Minimize material wastage by catching errors early.
7. Split the Design (If Necessary)
For machines with smaller embroidery hoops, splitting the design is essential. Use your digitizer for embroidery to:
- Divide the design into overlapping sections for seamless results.
- Align registration marks to ensure accuracy during stitching.
8. Stabilize the Fabric
Proper stabilization prevents fabric shifting and distortion. Use:
- Cutaway Stabilizers: For stretchy fabrics or dense designs.
- Tearaway Stabilizers: For less complex designs on stable fabrics.
- Consider basting stitches or adhesive sprays for additional support.
9. Pay Attention to Sequencing
Sequencing determines the stitching order of the design. Follow these tips:
- Start with the underlay, then move to the main elements and outlines.
- Prioritize larger sections before smaller details to maintain alignment.
- Ensure overlapping elements are stitched in a logical order.
10. Maintain Your Embroidery Machine
A well-maintained machine is critical for large designs. Regularly:
- Clean the bobbin case and replace worn-out needles.
- Use high-quality threads suitable for large-scale projects.
- Ensure correct thread tension for smooth and consistent stitching.
Benefits of Professional Digitization for Large Designs
Hiring an expert digitizer for embroidery ensures:
- Flawless Results: Avoid common pitfalls like thread breaks and misalignments.
- Time Savings: Focus on other aspects of your business or project.
- Access to Advanced Techniques: Professionals bring expertise in handling complex elements like gradients and textures.
FAQs
1. What software is best for digitizing large embroidery designs?
Software like Wilcom, Hatch Embroidery, and Brother PE-Design offer robust features for handling large-scale projects.
2. How do I prevent fabric puckering in large designs?
Use proper stabilization techniques, adjust stitch density, and ensure the fabric is hooped tightly.
3. Can I digitize large designs on my own without professional help?
Yes, with practice and the right tools, you can digitize embroidery designs. However, for complex projects, hiring a professional digitizer can save time and ensure quality.
4. What is the best way to split a large design for smaller hoops?
Use your software’s splitting tool to divide the design into overlapping sections. Align registration marks carefully during stitching.
5. How do I ensure smooth shading in large embroidery designs?
Adjust stitch density gradually to create gradient effects. Test the design on fabric to ensure consistency.