Essential Maintenance Tips for Maximizing Industrial Equipment
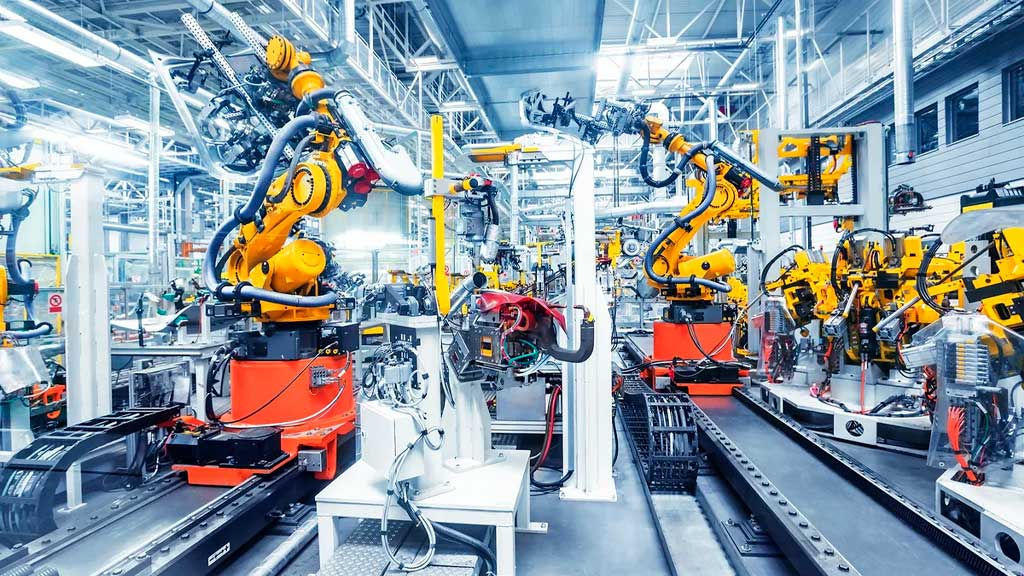
The longevity and reliability of equipment are crucial for maintaining productivity and minimizing downtime. Proper maintenance not only extends the lifespan of machinery but also enhances operational efficiency and safety. Here are essential maintenance tips to help maximize the lifespan of your industrial equipment.
Regular Inspections
Industrial Equipment, Conducting routine inspections is vital for identifying potential issues before they escalate into significant problems. Develop a schedule for checking critical components, such as bearings, belts, and electrical connections. Use checklists to ensure that all essential aspects are covered during each inspection.
Key Points:
- Inspect for wear and tear, leaks, or unusual noises.
- Use vibration analysis and thermography to detect hidden issues.
- Document findings to track trends over time.
Preventive Maintenance Programs
Implement a preventive maintenance (PM) program tailored to your equipment. PM involves regular, scheduled maintenance tasks aimed at preventing equipment failure. This proactive approach can significantly reduce downtime and repair costs.
Key Points:
- Set specific intervals for tasks such as lubrication, filter changes, and part replacements.
- Use maintenance management software to automate scheduling and track completed tasks.
- Ensure all staff are trained in PM practices and understand their importance.
Proper Lubrication
Lubrication is critical to reducing friction and wear on moving parts. Establish a lubrication schedule based on manufacturer recommendations and the operational environment.
Key Points:
- Use the right type and grade of lubricant for each application.
- Clean lubricating surfaces to avoid contamination.
- Monitor lubricant levels and conditions regularly.
Training and Awareness
Educate your staff on proper equipment operation and maintenance procedures. Well-trained employees are less likely to misuse equipment, reducing wear and potential damage.
Key Points:
- Conduct regular training sessions and refreshers on equipment handling.
- Encourage employees to report any irregularities or concerns promptly.
- Foster a culture of safety and responsibility regarding equipment care.
Utilize Technology
Embrace technology to enhance maintenance efforts. Predictive maintenance tools, such as IoT sensors and monitoring systems, can provide real-time data on equipment performance.
Key Points:
- Implement condition monitoring systems to assess equipment health.
- Analyze data trends to predict when maintenance is needed.
- Use software solutions for scheduling, tracking, and reporting maintenance activities.
Cleanliness and Environment
Maintaining a clean work environment is essential for preventing contamination and damage to equipment. Dust, dirt, and debris can lead to malfunctions and decreased efficiency.
Key Points:
- Establish regular cleaning routines for equipment and work areas.
- Ensure proper storage for tools and materials to avoid clutter.
- Control environmental factors, such as temperature and humidity, that could impact equipment.
Adhere to Manufacturer Guidelines
Always follow the manufacturer’s maintenance guidelines and recommendations. These guidelines are designed to optimize performance and extend equipment lifespan.
Key Points:
- Keep documentation and manuals accessible for reference.
- Schedule maintenance tasks based on the manufacturer’s suggested intervals.
- Use genuine parts and components to ensure compatibility and reliability.
Monitor Performance Metrics
Tracking key performance indicators (KPIs) related to equipment can help identify patterns and areas for improvement. Metrics such as uptime, downtime, and maintenance costs are essential for evaluating the effectiveness of your maintenance program.
Key Points:
- Establish a baseline for normal performance to identify anomalies.
- Regularly review and analyze performance data.
- Adjust maintenance strategies based on insights gained from performance metrics.
Address Issues Promptly
RINA SRP Series, address them immediately to prevent further damage. Delaying repairs can lead to more extensive and costly problems down the line.
Key Points:
- Establish a clear reporting procedure for equipment issues.
- Prioritize repairs based on severity and impact on operations.
- Document all repairs and maintenance activities for future reference.
Plan for Replacement
Despite best efforts, all equipment will eventually reach the end of its useful life. Developing a replacement plan ensures that you’re prepared for equipment failures without disrupting operations.
Key Points:
- Assess the age and condition of equipment regularly.
- Budget for replacements and upgrades in advance.
- Research newer technologies that may enhance efficiency or reduce operational costs.
Conclusion
Maximizing the lifespan of industrial equipment requires a comprehensive approach that includes regular inspections, preventive maintenance, employee training, and the use of technology. By implementing these essential maintenance tips, businesses can enhance equipment reliability, improve productivity, and reduce costs associated with unexpected breakdowns. A proactive maintenance strategy not only extends the life of machinery but also contributes to a safer and more efficient workplace.