The Future of Injection Molding: Trends and Innovations
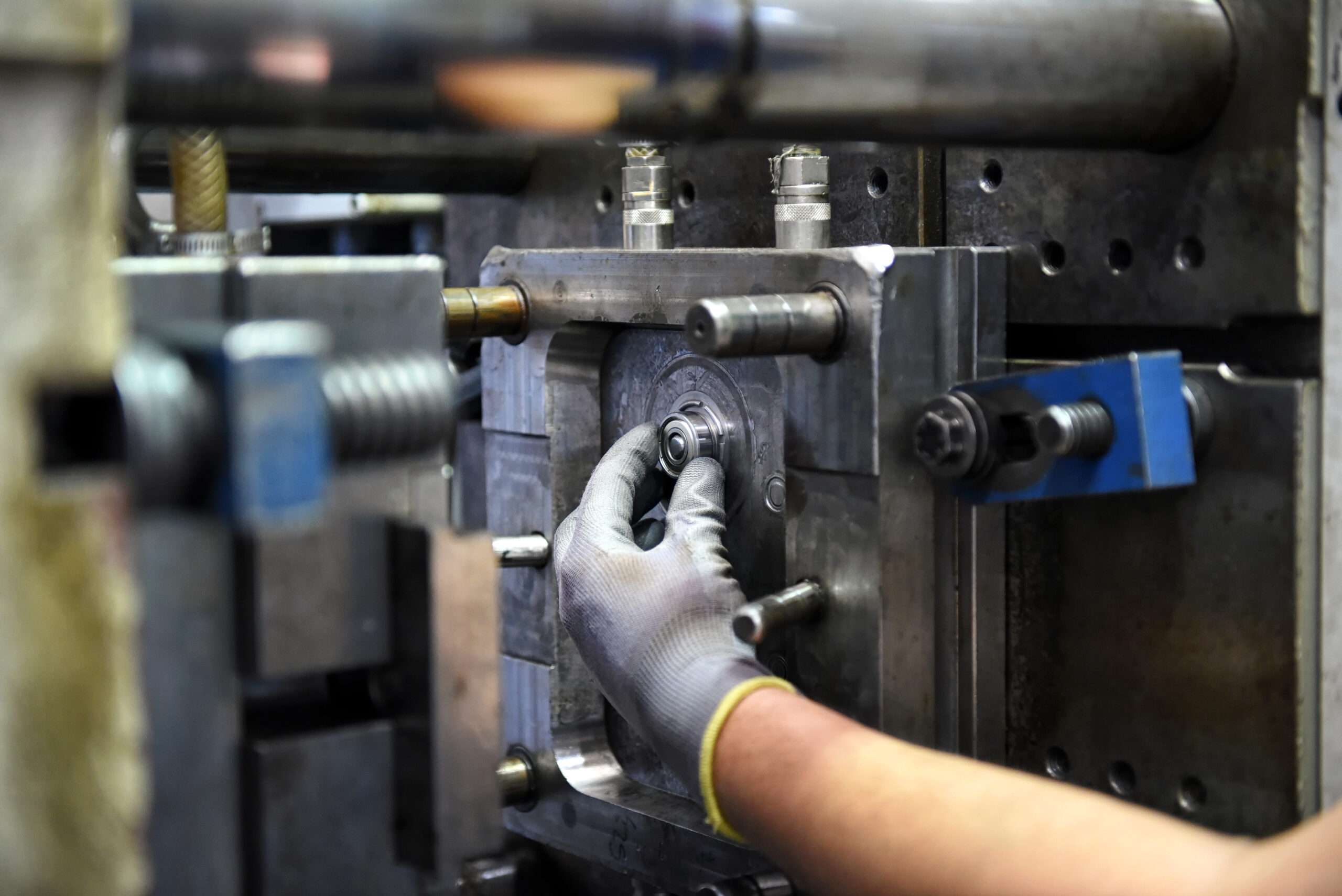
The Future of Injection Molding: Trends and Innovations
Injection molding has long been a cornerstone of the manufacturing industry, providing a reliable method for producing complex parts with high precision. As technology advances, the injection molding landscape continues to evolve, bringing forth new trends and innovations that enhance efficiency and product quality. In this article, we will explore these developments, their implications for businesses, and what the future holds for injection molding.
Understanding Injection Molding
Injection molding is a manufacturing process used to create parts by injecting molten material into a mold. This method is particularly favored for its ability to produce large quantities of identical items with minimal waste. The process typically involves several key steps:
- Material Selection: Choosing the right thermoplastic or thermosetting polymer is crucial for achieving desired properties.
- Melt and Inject: The selected material is heated until it becomes molten and is then injected into a mold under high pressure.
- Cooling and Solidifying: Once the material fills the mold, it cools and solidifies, taking on the shape of the mold.
- Ejection: After cooling, the molded part is ejected from the mold.
This efficient process allows manufacturers to produce a wide range of products, from automotive components to consumer goods.
Key Benefits of Injection Molding
Injection molding offers numerous advantages, making it a preferred choice for many manufacturers. Here are some key benefits:
- High Efficiency: The process allows for rapid production, making it ideal for large-scale manufacturing.
- Cost-Effectiveness: Although the initial investment in molds can be high, the cost per part decreases significantly with larger production runs.
- Design Flexibility: Manufacturers can create complex shapes and designs that would be difficult or impossible with other methods.
- Material Variety: A wide range of materials can be used, including various plastics and even metals.
These benefits contribute to the ongoing popularity of injection molding across multiple industries.
Current Trends in Injection Molding
As the industry evolves, several trends are shaping the future of injection molding. Here are some notable developments:
1. Automation and Robotics
Automation is transforming the injection molding process. By integrating robotics, manufacturers can enhance precision and reduce labor costs. Robots can handle tasks such as:
- Loading and unloading materials: This streamlines the production process.
- Quality inspection: Automated systems can quickly identify defects, ensuring high-quality output.
- Packaging: Robots can efficiently package finished products, further speeding up production.
2. Sustainable Practices
Sustainability is becoming increasingly important in manufacturing. Injection moulding companies are adopting eco-friendly practices, including:
- Recycling materials: Many manufacturers are now using recycled plastics to create new products.
- Energy-efficient machines: Investing in energy-efficient equipment reduces overall energy consumption.
- Reducing waste: Innovations in design and production techniques aim to minimize material waste during the molding process.
3. Advanced Materials
The development of advanced materials is revolutionizing injection moulding. New materials offer improved performance characteristics, such as:
- Lightweight composites: These materials reduce the weight of parts without sacrificing strength.
- Biodegradable plastics: As consumers demand more sustainable options, biodegradable materials are gaining traction.
- High-performance polymers: These materials withstand extreme temperatures and pressures, making them suitable for specialized applications.
4. Industry 4.0 Integration
The integration of Industry 4.0 technologies is reshaping the injection molding landscape. This includes:
- IoT (Internet of Things): Sensors embedded in machines provide real-time data on production processes, allowing for better monitoring and optimization.
- Big Data Analytics: Analyzing production data helps manufacturers identify inefficiencies and improve processes.
- Predictive Maintenance: Using data analytics can predict equipment failures before they occur, reducing downtime.
5. Customization and Short Runs
As consumer preferences shift toward personalized products, manufacturers are responding by offering customization options. Injection moulding is adapting to support:
- Short production runs: Advanced technologies enable cost-effective production of smaller quantities.
- Tailored designs: Manufacturers can easily modify existing molds to create unique products.
Challenges Facing the Injection Molding Industry
Despite its many advantages, the injection moulding industry faces several challenges. Addressing these issues is crucial for sustaining growth and innovation.
1. Rising Material Costs
The cost of raw materials can fluctuate significantly, impacting overall production costs. Manufacturers must find ways to manage these expenses while maintaining quality.
2. Skilled Labor Shortage
As technology advances, the need for skilled workers who can operate and maintain sophisticated machinery increases. Companies must invest in training programs to develop the necessary skills in their workforce.
3. Environmental Regulations
With growing concerns over environmental impact, manufacturers must comply with stricter regulations regarding waste management and emissions. Adopting sustainable practices is essential for meeting these requirements.
Table: Comparison of Injection Molding Trends
Trend | Description | Impact on Industry |
---|---|---|
Automation and Robotics | Integration of robotics for efficiency | Reduces labor costs and increases precision |
Sustainable Practices | Adoption of eco-friendly methods | Enhances brand reputation and compliance |
Advanced Materials | Use of innovative materials | Improves product performance |
Industry 4.0 Integration | Implementation of IoT and data analytics | Optimizes production processes |
Customization and Short Runs | Support for personalized products | Meets changing consumer demands |
Future Outlook for Injection Molding
The future of injection molding looks promising, driven by technological advancements and changing market demands. As manufacturers continue to innovate, the following trends are likely to shape the industry:
1. Increased Automation
The trend toward automation will likely accelerate, with more manufacturers adopting robotic systems to enhance efficiency and reduce human error.
2. Greater Focus on Sustainability
Sustainability will remain a priority, with companies increasingly adopting eco-friendly materials and practices to meet consumer expectations and regulatory demands.
3. Enhanced Customization Options
As consumer preferences shift toward personalized products, injection molding will evolve to support greater customization, allowing manufacturers to cater to individual needs.
4. Continued Material Innovation
Research and development in material science will lead to the creation of new, advanced materials that offer superior performance and sustainability.
5. Global Market Expansion
As manufacturing capabilities improve, businesses will seek to expand their reach into emerging markets, driving growth in the injection molding sector.
Conclusion
Injection molding remains a vital component of modern manufacturing, with its ability to produce high-quality parts efficiently. As the industry adapts to new trends and challenges, the focus on automation, sustainability, and customization will play a crucial role in shaping its future.
For businesses looking to stay competitive, it is essential to keep abreast of these developments and consider how they can implement innovative practices. To explore more about injection molding solutions, consider searching for options like injection molding services nearby or researching top manufacturers in China for injection molds. Embracing these changes will ensure that manufacturers not only survive but thrive in the ever-evolving landscape of injection molding.